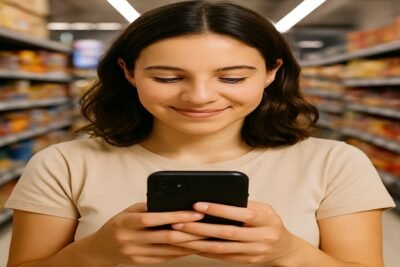
Manutenção Preventiva: Garantindo a Segurança e Eficiência
Quando pensamos no bom funcionamento de equipamentos, veículos ou sistemas industriais, a manutenção preventiva surge como uma das principais estratégias para evitar falhas inesperadas.
Mais do que corrigir problemas, ela visa antecipá-los, garantindo maior segurança nas operações e prolongando a vida útil dos ativos.
Trata-se de um investimento que, a longo prazo, traz benefícios financeiros e operacionais e estruturais.
Testes, Treinamento e Tecnologia a Favor da Segurança e Eficiência
A segurança e eficiência em um ambiente industrial dependem fortemente da manutenção adequada dos equipamentos.
Um dos principais componentes deste programa é a realização de testes periódicos.
Esses testes devem incluir inspeções visuais e operacionais, testes funcionais e, quando necessário, exames mais profundos, como a ultrassonografia e a termografia.
Cada equipamento deve ter um cronograma específico, considerando o tipo de operação e as condições a que está exposto.
É fundamental o treinamento contínuo das equipes responsáveis pela operação e manutenção.
Programas de capacitação ajudam a garantir que os operadores possuam as habilidades necessárias para identificar problemas com antecedência.
Um operador bem-treinado pode ser a primeira linha de defesa contra falhas potencialmente catastróficas.
A adoção de tecnologia no processo de manutenção também tem se mostrado uma estratégia eficaz.
Sistemas de monitoramento em tempo real podem enviar alertas sobre condições anormais, permitindo intervenções rápidas.
Isso aumenta a segurança e melhora a eficiência operacional, pois as intervenções podem ser programadas, evitando paradas inesperadas.
A manutenção adequada não se limita apenas a reduzir custos, mas também contribui para a sustentabilidade do negócio a longo prazo.
Manter os equipamentos em ótimo estado diminui o consumo de energia e reduz resíduos, um aspecto importante em um mundo cada vez mais preocupado com a sustentabilidade ambiental.
Importância da Inspeção Regular em Sistemas de Pressão
A integridade e a segurança de sistemas de pressão são fundamentais em diversas indústrias, desde a petroquímica até a energia.
Esses sistemas operam em condições críticas, tornando a inspeção regular uma prática imprescindível.
A falha em realizar inspeções pode resultar em acidentes graves, danos materiais e até mesmo perda de vidas.
A principal função da inspeção regular é identificar problemas antes que se tornem críticos. Isso inclui verificar vazamentos, desgastes em componentes e a integridade estrutural dos equipamentos.
Medidas preventivas, como o teste hidrostático em vasos de pressão, são essenciais para garantir que os sistemas operem de maneira segura e eficaz.
Os testes confirmam a resistência do material e a capacidade de suportar altas pressões, evitando falhas catastróficas.
Outro aspecto importante é a conformidade com normas e regulamentações de segurança.
Essas diretrizes exigem que as empresas realizem inspeções periódicas para garantir que todos os equipamentos atendam aos padrões de segurança.
Essa conformidade protege os trabalhadores e reduz o risco de responsabilidade legal para as empresas.
A tecnologia certamente desempenha um papel crescente nas inspeções.
Ferramentas como drones, sensores e câmeras térmicas proporcionam um novo nível de monitoramento.
Essas ferramentas permitem uma análise mais detalhada e precisa da condição dos sistemas, possibilitando intervenções rápidas e informadas.
A documentação das inspeções e manutenções é vital.
Manter registros precisos ajuda a rastrear o histórico dos equipamentos e a tomar decisões mais acertadas sobre o gerenciamento de ativos.
Isso pode resultar em economia de custos a longo prazo, além de melhorar a eficiência operacional.
Por fim, a cultura de segurança dentro das organizações deve valorizar e priorizar as inspeções regulares.
Treinamentos e conscientização sobre a importância dessas práticas são fundamentais para que todos os colaboradores entendam seu papel na manutenção da segurança no ambiente de trabalho.
Otimização de Equipamentos para Aumentar a Produtividade
A otimização de equipamentos é fundamental para qualquer setor que busca melhorar sua produtividade e eficiência operacional.
A implementação de estratégias eficazes pode transformar a forma como os recursos são utilizados, resultando em uma redução de custos e um aumento na produção.
Um dos principais fatores nessa otimização é a manutenção preventiva adequada dos equipamentos.
Isso evita falhas inesperadas e garante que o maquinário funcione em níveis ideais.
A adoção de tecnologias modernas, como sensores IoT e sistemas de monitoramento em tempo real, permite que as empresas analisem o desempenho dos equipamentos e identifiquem áreas que necessitam de melhorias.
Esses dados, quando utilizados corretamente, podem direcionar investimentos para atualizações ou substituições de equipamentos que estão impactando negativamente a eficiência.
Entre os componentes essenciais para a otimização estão os seguintes:
- Treinamento de funcionários;
- Atualização tecnológica;
- Análise de dados;
- Tomada de força para caçamba.
Um exemplo prático de otimização se destaca na construção civil, onde a tomada de força para caçamba permite que maquinários trabalhem de forma mais eficiente, melhorando a movimentação e o descarregamento de materiais.
Sistemas de gestão integrados podem unir informações de diversos setores, permitindo uma visão holística da operação.
Essa integração facilita a identificação de gargalos e otimizações em um único equipamento e em toda a cadeia produtiva.
Soluções Inovadoras para Processos Industriais Modernos
A indústria contemporânea tem sido profundamente impactada pela digitalização e inovação tecnológica, resultando em processos altamente otimizados.
Para atender à crescente demanda por eficiência e qualidade, muitas empresas têm adotado soluções inovadoras que incluem automação, Internet das Coisas (IoT), e inteligência artificial.
A automação é um dos pilares fundamentais da modernização industrial.
A implementação de robôs em linhas de produção não só reduz o erro humano, como também aumenta a velocidade de produção e diminui custos operacionais.
Outro aspecto crucial é a integração da IoT nos processos industriais.
Essa tecnologia permite que equipamentos e máquinas estejam conectados à rede, possibilitando a coleta de dados em tempo real.
A partir da análise desses dados, gestores podem prever falhas e otimizar manutenções, resultando em operações mais confiáveis.
A inteligência artificial (IA) também se destaca, permitindo a análise de grandes volumes de dados para tomada de decisões mais assertivas.
Aplicação de algoritmos de aprendizado de máquina em processos industriais ajuda a identificar padrões e prever resultados, tornando a produção mais eficiente e a utilização de recursos mais sustentável.
Além disso, tecnologias como impressão 3D e manufatura aditiva revolucionam produzir componentes, facilitando a customização e reduzindo desperdícios.
Essa abordagem diminui notavelmente os prazos de entrega e os custos associados à produção tradicional.
A personalização em massa, possibilitada por métodos ágeis e flexíveis, também é uma tendência crescente.
Os clientes exigem produtos que atendam suas necessidades específicas, e as fábricas modernas estão se adaptando rapidamente a essa demanda.
Investimentos em serviços de tornearia mecânica para a produção de componentes especializados são cada vez mais frequentes.
Esses serviços garantem precisão e qualidade em peças fundamentais, contribuindo para a competitividade no mercado.
Por fim, camadas de segurança cibernética são indispensáveis, uma vez que a digitalização também traz à tona novos riscos.
A proteção de dados operacionais tornou-se uma prioridade fundamental, exigindo soluções robustas para garantir a integridade dos sistemas e informações.
A Relevância da Manutenção Preventiva em Ambientes Industriais
A manutenção preventiva é um aspecto crucial para a eficiência e longevidade dos equipamentos industriais.
Seu objetivo é identificar e corrigir potenciais falhas antes que elas se tornem problemas sérios, o que pode resultar em paradas inesperadas e prejuízos financeiros significativos.
Um dos principais benefícios da manutenção preventiva é a melhoria da segurança no ambiente de trabalho.
Equipamentos que estão em boas condições de funcionamento apresentam menor risco de acidentes.
A manutenção regular dos maquinários, por exemplo, garante que todos os componentes estejam operando conforme as especificações do fabricante, minimizando o risco de falhas catastróficas.
A manutenção preventiva também contribui para a eficiência energética.
Equipamentos operando de forma otimizada consomem menos energia, resultando em redução de custos e um impacto ambiental menor.
Um exemplo claro é a torre de refrigeração industrial, que deve ser mantida adequadamente para evitar desperdícios de energia devido a falhas no sistema de resfriamento.
Outro aspecto importante é a continuidade da produção.
A manutenção preventiva assegura que as máquinas estejam sempre disponíveis e prontas para uso, evitando interrupções na linha de produção que podem afetar a entrega de produtos e a satisfação do cliente.
Por último, a manutenção preventiva pode prolongar a vida útil dos equipamentos.
Ao evitar o desgaste excessivo e mantendo as máquinas em boas condições, as empresas podem adiar a necessidade de investimentos em novos equipamentos, o que é uma vantagem financeira significativa.
Espero que o conteúdo sobre Manutenção Preventiva: Garantindo a Segurança e Eficiência tenha sido de grande valia, separamos para você outros tão bom quanto na categoria Blog
Conteúdo exclusivo